Is GaN the future for EV chips?
Gallium Nitride technology aims to replace silicon and boost electric-vehicle performance while cutting cost.
This article by Paul Wiener was published in full 4/22/21 on SAE.Org. Read the full, unabridged article here, complete with reference gallery.
Technology advances in electric vehicles (EV) are steadily shrinking the vehicle bill-of-materials cost while creating power efficiencies and new design solutions. The combination of more power-dense batteries and higher-efficiency electric motors, inverters and onboard chargers is helping to reduce vehicle mass, resulting in greater range.
For this reason, EV propulsion-system developers are bringing gallium nitride (GaN) power transistors into greater focus. GaN has the potential to replace silicon as the heart of electronic chips, to satisfy a growing need for faster, more-efficient circuits in high-power environments. GaN is capable of sustaining higher efficiency than silicon; GaN semiconductors have 1,000 times more electron mobility – they flow faster – than silicon. This, in turn, provides improved thermal-management conditions, resulting in smaller and lower-cost system cooling options.
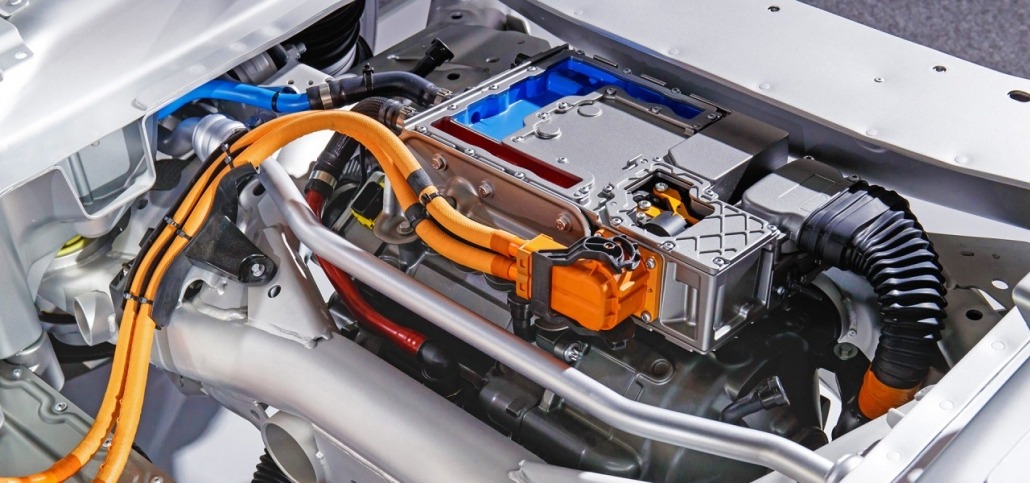
EV power electronics, as shown on the Jaguar I-Pace, offer significant applications for GaN semiconductors. (Jaguar)
As with most new technologies, there is a time period between early adoption and mainstream use. GaN currently is at that tipping point into mainstream. Proven reliability, manufacturing advances and government regulations for higher efficiency and lower CO2 emissions all have led to customer demand for GaN.
GaN FETs (field-effect transistors, which use an electric field to control the flow of current) offer potential for higher efficiency and power density in EV traction inverters, onboard chargers (OBC) and DC/DC converters.
GaN-based inverters deliver efficiency improvements of more than 70% compared to today’s inverters using traditional IGBT (insulated-gate bipolar transistor) semiconductors that currently are the workhorses in EV and hybrid vehicle power control.
DC-to-DC power conversion is needed from a vehicle’s battery to support multiple low-voltage systems such as HVAC and power steering. As in the case of the inverter, GaN power semiconductors can increase power conversion efficiency by 50% and enable size and weight reductions up to 33%. The accrued increase in efficiency and reductions in size and weight of OBCs, traction inverters and DC/DC systems in an EV helps deliver greater driving range with current battery capabilities and more package efficiency.
Subsystem benefits of GaN
The following examples provide an overview of how GaN is implemented in EV powertrain functions, as well as the efficiency and power-density benefits of GaN-based systems:
- Onboard charger: GaN power semiconductors contribute to more space-efficient propulsion-system designs, opening up new volume for other vehicle components with OBC integration.
- DC/DC converter: Power conversion (e.g. 400V-to-12V or 48V-to-12V) from the vehicle battery is needed to support accessory systems with low voltage needs. The diagrams illustrate a typical GaN layout and corresponding benefits in size and efficiency.
- Traction inverter: While an EV’s propulsion system (traction inverter plus electric motor) is five times more energy efficient than IC engines, with lower maintenance costs and longer lifespan, the upfront cost has on average been 2.5 times higher. Technology innovation in materials, magnetics and electronics is creating new-generation motors that are more energy efficient (less power loss through heat), compact and lighter in weight. GaN power semiconductors are key to the evolution of traction inverters capable of delivering more than a 70% power increase compared to inverters using traditional IGBTs.
Increased efficiency and decreased power-system size and weight will enable EVs to drive further even without any change in current battery capabilities. Comparison testing conducted in 2020 by GaN Systems, in partnership with a customer, showed that the efficiency of a GaN-based traction inverter is improved significantly by reducing power losses by 50%, resulting in battery energy saving – and ultimately extended driving range.
Using Tesla Model S as an example (curb weight: 2,200kg/4,850 lb.; battery capacity: 75 kWh; inverter max power: 200kW; 400V battery systems), the mileage can be estimated based on two driving scenarios. One scenario is with constant 60 km/h (37 mph) speed, the other is based on the Worldwide Harmonized Light-vehicle Test Procedure (WLTP) Class 3b driving cycle. With the GaN-based inverter, the driving range is extended 6-10% compared to a conventional Si IGBT traction inverter.
Another perspective is the system cost reduction with the GaN-based traction inverter. With energy saving and high efficiency, the battery capacity can be reduced for the same driving range per one charging cycle. The accompanying chart derived from the 2020 testing compares the ΔT results between GaN and IGBT transistors at different power loads. With a lower ΔT (Tj-Tfluid) cooling system (approximately 20°C difference), the GaN solution reduces the volume of the cooling system size by 40%, resulting in significant cost savings. Additionally, with GaN system running at cooler temperatures, system reliability and longevity is enhanced.
Read the rest of the article, where Paul Wiener compares GaN vs. SiC here.